News
Site Editor
Site
https://kitechpm-3e93b2.cdngin.com/uploads/image/60c9c2b19951d.png
Control Moisture Content in Plastic Pellets for Maximum Product Quality
Views: 260
Author: Site Editor
Publish Time: 2025-06-30
Origin: Site
Plastic pellet moisture control is one of the most significant parameters with direct impact on the final quality and performance of the plastic product. Uncontrolled pellets may lead to some of the following problems in extrusion or molding processes such as surface defects, voids, loss of mechanical strength, and even equipment failure. For plastic pelletizing equipment operators who are recyclers and processors, ideal moisture content is not only a matter of product uniformity concern—it's the secret to trouble-free operation, consistent product, and happy customers. In this article, the primary reasons for moisture in plastic pellets are presented, effective ways of detecting it, and efficient means in managing and eliminating moisture in pelletizing.
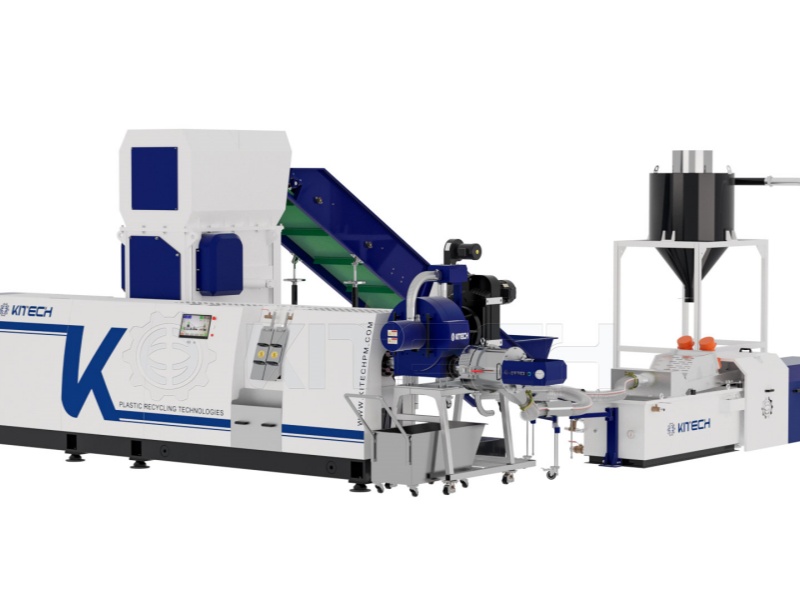
1.Why Is Moisture Content in Plastic Pellets Critically Important?
Humidity level in plastic pellets is quite crucial in preserving the quality, consistency, and functionality of final plastic products. Either from virgin polymers or from recycled plastics, the right moisture content during production using a plastic pellet making machine is quite crucial.
1.1 Impact on Downstream Processing
If your plastic pellets are not dry, there can be encountered various kinds of downstream processing problems in injection molding, extrusion, or blow molding:
·Surface Defects
Too much moisture causes splay marks, pitting, and bubbles, which result in the deterioration of the end product's appearance and functionality.
·Internal Voids and Structural Deficiencies
Moisture trapped inside is turned to steam when melted, creating bubbles and voids, which lower the structural integrity of the part.
·Burn Marks are Degradation of Color
Flash of vapor during high-temperature processing will result in local overheating, generating black spots and discoloration.
·Poor Mechanical Properties
Water hinders polymer bonding such that parts become brittle or tensile strength is compromised.
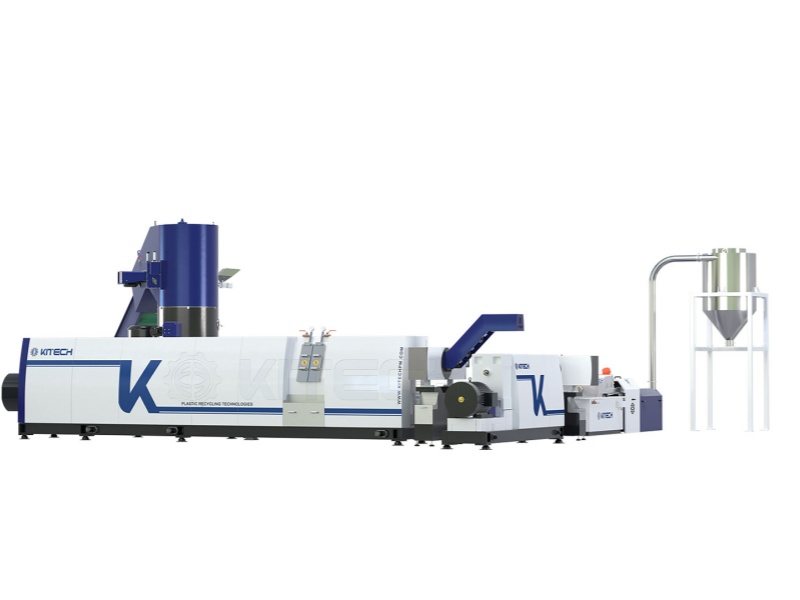
1.2 How It Affects Production Efficiency
Processing a plastic pellet manufacturing machine without moisture control causes process interruptions and productivity inefficiencies on an ongoing basis:
·Material blocking of feed systems
·Unstable melt flow due to vapor expansion
·Increased cycle times due to cooling imbalances
Decreased equipment lifespan due to thermal stress
Equivalent moisture content must be maintained in order to assist in protecting your plastic pellet manufacturing machine and offer consistent production with less downtime.
1.3 Common Moisture Sources in Pelletizing
Moisture Source | Typical Issue | Impact |
Wet raw materials | Vapor bubbles, weak bonding | Defective finished products |
Incomplete drying before extrusion | Steam formation, burn marks | Visual and structural defects |
High humidity during storage | Reabsorption of moisture after pelletizing | Leads to out-of-spec pellets |
Inefficient cooling and dehydration | Residual moisture in final pellets | Limits application range and shelf life |
2.What Are the Primary Sources of Moisture in Plastic Pellets?
In making plastic pellets, particularly through the operation of a plastic pellet making machine, there are several points of moisture introduction at many places—most of which are easily overlooked. Suppliers these have a critical role to play in preventing processing issues as well as assuring regular pellet quality.
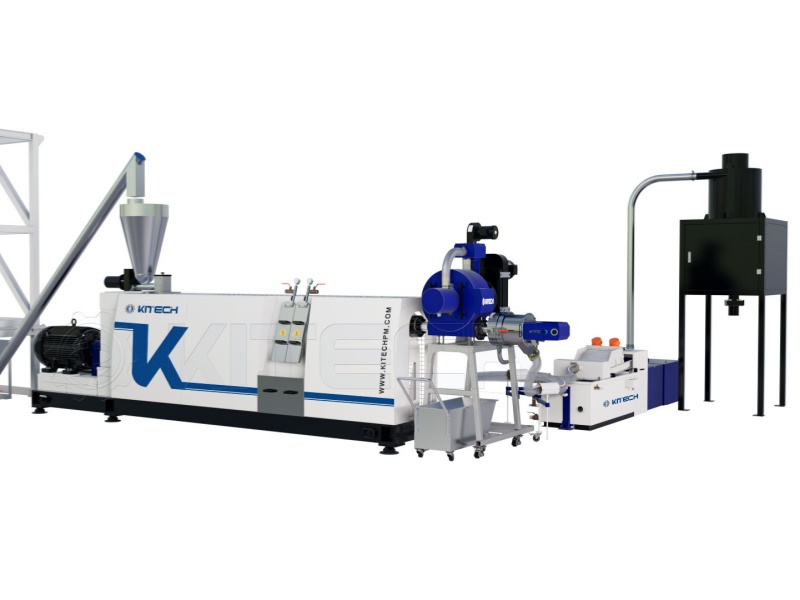
2.1 Moisture in Recycled Raw Materials
There is most typically recycled plastic. Post-industrial and post-consumer material will typically include rainwater, moisture, or residue of a previous use. These are hygroscopic materials with a built-in moisture that must be removed by high temperatures. Putting wet material into a plastic pellet machine without processing results in poor-quality pellets and downstream failure.
2.2 Incomplete Drying After Washing
Products are deimpure in most of the operations. But if the subsequent drying process following washing is not successful, surface and internal moisture will be trapped. Centrifugal dryers or hot air plants can fail to extract moisture—especially when throughputs are high. Excess water is a significant problem when supplemented at the plastic pellet making machine, leading to foaming, pressure fluctuation, and irregular pellets.
2.3 High Humidity in Storage and Handling Areas
Even with drying, plastic flakes and pellets can reabsorb water from the air if in open containers, open storage bins, or in non-climate-controlled warehouses. The culprits are open containers, uncovered storage bins, or non-climate-controlled warehouses. Reabsorption happens when the surrounding air is too humid, making even good quality processed pellets unusable for molding or extrusion except for re-drying.
2.4 Inadequate Cooling and Dehydration After Pelletizing
All plastic pellet-making equipment uses water to cool molten plastic or plastic strands extruded prior to cutting. Water adheres to pellets without dehydration, i.e., high-speed centrifugal dryers, vacuum dryers, or air knives. This is especially troublesome for underwater pelletizing systems or water-ring pelletizers where incomplete evaporation of water directly affects pellet quality and shelf stability.
2.5 Leaking or Outdated Equipment
Less obvious, but equally worthwhile sources of moisture are old or neglected drying and conveying equipment. Dryer vessels with perforated walls, broken seals, or low air flow velocities can all lose the moisture-removal ability. Some plants, inefficient components in, can introduce more moisture than they extract—undermining even the best plastic pellet making machine efficiency.
2.6 Table: Common Moisture Sources in Plastic Pellet Production
Moisture Source | Description | Process Stage |
Recycled plastic raw materials | Inherent moisture from storage or previous use | Pre-processing |
Incomplete drying after washing | Residual moisture not removed by drying systems | Pre-processing |
Humid storage conditions | Reabsorption from high-humidity environments | Post-drying / storage |
Poor dehydration after cooling | Inefficient drying after water-cooled pelletization | Post-pelletizing |
Aging or faulty drying equipment | Leaks, low performance, or poor maintenance | Pre- and post-pelletizing |
The secret to enhancing pellet quality, enhancing the consistency of your production, and minimizing scrap material is determining where moisture is gaining access into your plastic pellet manufacturing process. The following section will cover how best and most successfully to measure moisture content.
3.How to Measure Moisture Content in Plastic Pellets?
Proper measurement of plastic pellet moisture content must be ensured to obtain a consistent and efficient operation of a plastic pellet production machine. Deterioration, inadequate mechanical performance, or outright rejection in subsequent injection molding or extrusion operations may result from lack of control in moisture content. Fortunately, several common detection and measurement methods of plastic pellet moisture content are available.
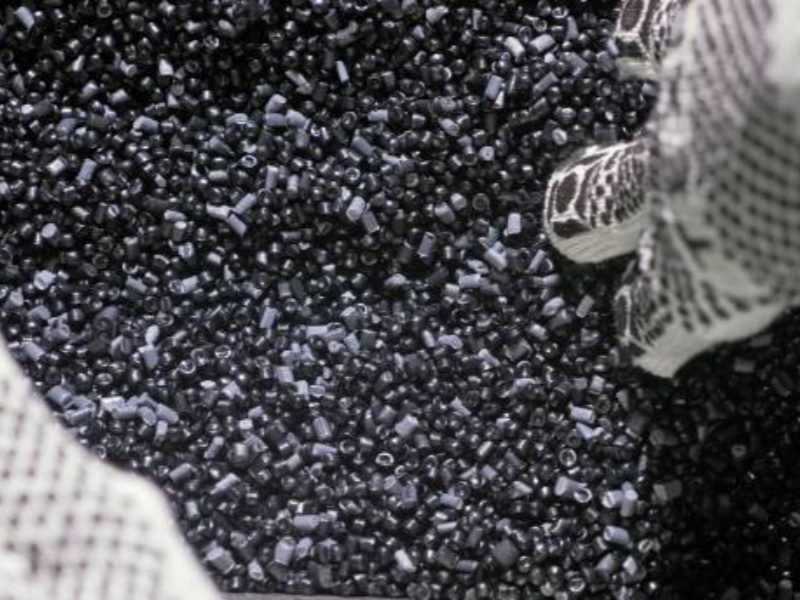
3.1 Infrared Moisture Analyzers (IR)
Infrared (IR) moisture analyzers are common due to their simplicity of use and speed. IR analyzers operate on the principle of infrared radiation heating a sample, where loss in weight on driving off water content as vapor is measured. IR analyzers suit rapid site measurement and are typically situated at the front of plastic pellet production machine lines for regular quality monitoring.
·Advantages: Rapid turnaround times (typically 2–5 minutes), non-destructive, user-friendly interface
·Limitations: Not very accurate at extremely low moisture levels (<0.01%), surface water-sensitive
3.2 Thermogravimetric Analysis (TGA) / Loss on Drying (LOD)
It is a gravimetric method in which weighed sample is ignited in the oven and weight loss is recorded. It is a very traditional method but gives quite good results.
·Advantages: Reliable for non-hygroscopic and hygroscopic materials, cost-effective
·Limitations: Slower (30–120 minutes), there is a need to precisely control drying temperature, not for on-line measurement
3.3 Karl Fischer Titration (KF)
Karl Fischer titration is an extremely accurate chemical quantitative trace analysis for water, especially less than 0.01%. Karl Fischer titration is a very mundane method used in the lab where maximum accuracy is needed.
·Advantages: Highly sensitive and accurate (±0.001%), ideally suited for high-risk use
·Restrictions: Trained operator, reagents, controlled lab environment necessary; not designed for in-line or on-site application
3.4 Online Moisture Sensors
For online measurement for mass production, the majority of manufacturers place online moisture sensors on their plastic pellet manufacturing machine lines. The sensors utilize NIR (Near-Infrared Reflectance) or microwave technology to continuously measure moisture without interfering with the production process.
·Advantages: Continuous, no-contact, allows automation and process enhancement
·Limitations: Costly to install at first, needs to be calibrated, and material density or color sensitive
3.5 Comparison Table: Moisture Detection Methods for Plastic Pellets
Method | Accuracy | Speed | Suitable For | On-line Capability | Cost |
Infrared Analyzer (IR) | ±0.1% | 2–5 min | Routine quality checks | Yes | Medium |
Thermogravimetric (LOD) | ±0.05% | 30–120 min | Lab-scale verification | No | Low |
Karl Fischer Titration | ±0.001% | 20–30 min | Ultra-low moisture, high precision | No | High (lab-only) |
Online NIR/Microwave Sensor | ±0.1–0.5% | Continuous | Real-time, high-volume production | Yes | High |
4.Effective Solutions to Reduce Moisture in Plastic Pellets
Plastic pellets with high moisture content can undermine downstream processing, affect mechanical performance, and lead to extensive material loss. To ensure the effective use of any machine to produce plastic pellets, manufacturers will have to implement efficient means of minimizing moisture that is sensitive to process design and equipment selection.
4.1 Use of High-Efficiency Dewatering Systems
In water-cooled pelletizing devices such as strand pelletizers and water-ring pelletizers, water removal after pellet cutting is necessary. A pellet machine has to be provisioned with centrifugal dryers at high speed, air knives, or vibrating fluidized bed dryers to eliminate surface moisture before conveying or packaging.
·Best Practice: Equip with a centrifugal dewatering unit of equal discharge capability to pellet output capacity to avoid backlogs or rewetting.
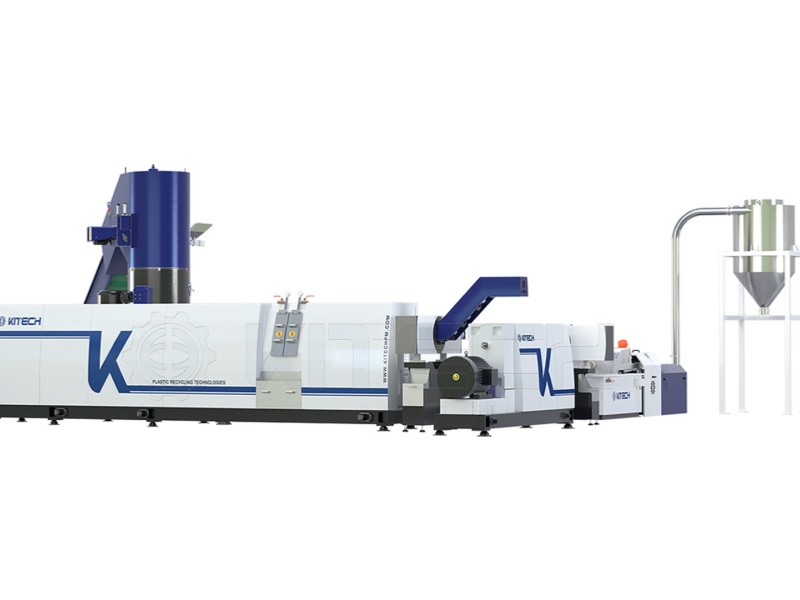
4.2 Implementation of Hot Air Drying Systems
For hygroscopic materials like PET or PA, surface drying alone is not adequate. In most uses, a hot air dryer, frequently used in conjunction with desiccant-based drying towers, can reduce internal moisture to below 0.05%. These devices can be equipped inline in front of material feeding into the plastic pellet making machine, or after pelletizing when there is a re-drying need.
·Case Example: PET bottle recycling plant saw 32% fewer injection mold defects following when they optimized their air drying stage from ambient air drying to closed-loop hot air drying.
4.3 Adoption of Vacuum Drying Technology
Vacuum dryers yield rapid, energy-conserving drying to extremely low terminal moisture levels. Equipment reduces water's boiling point when in a vacuum state, meaning drying is faster and less thermally harsh—ideal for heat-sensitive polymers.
·Ideal For: High-accuracy pellet production where the withdrawal of moisture is required to below 0.01% before processing further.
4.4 Immediate Cooling and Sealed Storage
Moisture control does not end with the pelletizing step. Dry pellets will, in fact, pick up moisture from around them if not properly protected. Pellets must be put into moisture-proof bags or sealed silos with controlled humidity immediately after they have cooled.
·General Mistake: Leaving pellets in uncovered pots in damp surroundings halts drying work completed, specifically for those that are produced on a plastic pellet manufacturing machine without drying after post-pelletizing.
4.5 Table: Summary of Moisture Reduction Techniques
Solution | Moisture Reduction Level | Suitable Material Types | Use Stage | Cost Level |
Centrifugal Dewatering | Surface moisture only | PE, PP, non-hygroscopic plastics | Post-pelletizing | Low |
Hot Air Drying (Desiccant) | < 0.05% | PET, PA, PC, hygroscopic plastics | Pre-/Post-pelletizing | Medium |
Vacuum Drying | < 0.01% | High-value engineering plastics | Pre-processing | High |
Sealed Storage & Packaging | Prevents moisture absorption | All plastic pellet types | Post-cooling | Low |
5.The Impact of Choosing the Right Pelletizing Equipment on Moisture Control
Proper machine selection to make plastic pellets determines ideal control of moisture during the pellet-making process. Equipment design parameters such as pellet cutting devices, cooling, and dehydrating efficiency all have a direct impact on the finished product's final moisture content.
5.1 Pellet Cutting Methods: Underwater vs. Strand Pelletizing
·Underwater Pelletizing
In this case, molten strands of polymer are sheared in water, which cools the pellets rapidly. Although giving good pellet shape and surface finish, the pellets will contain a significant amount of water on the surface and require adequate dehydration systems downstream to achieve low moisture content.
·Strand Pelletizing (Air Cooling):
Here, water or air bath cool molten strands prior to cutting. While this process will have the effect of reducing surface moisture when compared to underwater pelletizing, it will at times require longer cooling times and be less dense. It can produce lower pellet moisture but impact throughput.

5.2 Cooling Techniques and Their Role in Moisture Control
Cooling has a double effect: solidifying the pellets and conditioning residual moisture. Water-cooling operations, like underwater pelletizing, have excess moisture that must be eliminated effectively. Air cooling reduces water contact but is not feasible for all polymers or volumes.
5.3 Efficiency of Dehydration Equipment
The effectiveness of post-pelletizing drying hardware—centrifugal dryers, air knives, fluidized beds—is a significant contributor to end-pellet moisture. Proper design of a drying system as an accessory to the plastic pellet making machine output provides pre-drying before storage or packaging, and thus avoids downstream issues.
5.4 Comparison Table: How Pelletizing Equipment Affects Moisture Content
Equipment Feature | Impact on Moisture Control | Advantages | Considerations When Choosing |
Underwater Pelletizing | Higher surface moisture, requires strong drying | Good pellet shape, compact footprint | Need for efficient drying downstream |
Strand Pelletizing (Air Cooling) | Lower surface moisture due to air cooling | Reduced drying need, simpler water handling | Longer cooling time, larger equipment footprint |
Water Cooling | Adds moisture, must be combined with drying | Rapid pellet solidification | Requires reliable dewatering system |
Air Cooling | Minimizes moisture introduction | Energy-saving, less drying needed | Limited to certain polymers and capacities |
Centrifugal Dryer Efficiency | Directly reduces moisture on pellet surface | Quick and effective moisture removal | Match dryer capacity to pellet output |
Control of moisture in plastic pellets is as precise as it needs to be to make all the difference to best-quality output, minimized defects, and process stability. From identifying the source of excess moisture to investing in precise detection equipment and effective drying machinery, every step has a direct bearing in the pelletizing sector as a whole. Besides this, selecting a highly performing plastic pellet making machine with effective dehydration and cooling effect can even eliminate moisture issues from the very starting. With such pre-treatment of bottlenecks, manufacturers not only gain maximum performance of their products but also attain highest operating efficiency and achieve an even improved competitive edge in the highly competitive plastics industry.